INTEGRATED
CIRCUIT
ANALYSIS
Problem Statement
Wirebonds are essential components in Integrated Circuit (IC) as their failure can cause the IC to malfunction. Wirebonds can fail due to various modes of failure such as shear failure, fatigue failure, corrosion, and others. Industrial practices to prevent wirebond failure typically involve measures such as changing materials, quality control, or ultimately, disposing of the failed component. However, a more effective approach to avoid wirebond failure is to perform realistic and meticulous simulations on the IC to identify the root cause of failure. Such simulations can enable engineers to take preventive measures to ensure the reliability and performance of the IC.
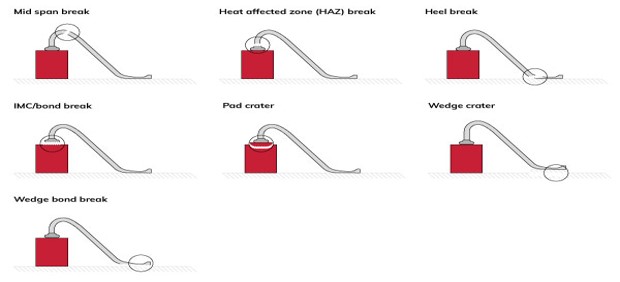
Digital Conversion and Twinning
Before conducting the simulation, a digital twin of the IC was created using Abaqus FEA. This involved generating a precise three-dimensional model with the aid of microscopic images and X-rays. The 3D model was then used to replicate the loading conditions and environments on the IC. In order to achieve higher accuracy, the mesh size used in IC design often goes below 1um and may even be further reduced, as micro parts are involved in the process.
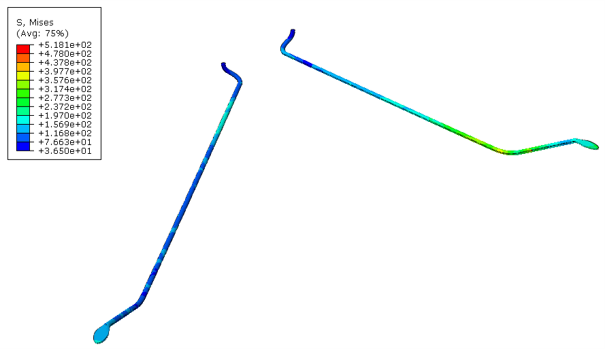


Environment Replication
To ensure the reliability and accuracy of FEA analysis in Abaqus FEA, the measurement environment was replicated using the digital twin of the IC. The material properties of the IC components were sourced from available literature. Comparison was made between results obtained from FEA analysis and measurement. The degree of matching between the two results serves as an indicator of the analysis accuracy.
Parameter Study
There are various factors that may cause wirebond failure, including wire diameter, wirebond path, bond shape, exit angle, and others. By conducting parameter sweep analyses, it is possible to easily identify the degree of impact of each parameter contributing to wirebond failure. The results yielded information on the distribution and concentration of stress, displacement, and strain on the wirebond when subjected to load. The chart shows that the material properties of wirebond affects the distribution and concentratioon of stress.



Optimization
Although the impact of individual parameters can be significant, it is important to consider the combinations of multiple parameters for a more realistic analysis. By analyzing different parameter combinations, one can determine the best combination that leads to optimal design of IC with high durability and sustainability. The results from such a realistic analysis are valuable in reducing the stress exerted on the wirebond up to 50% from the original design. By incorporating I-Sight into the process, manual efforts are minimized, and the exploration of design spaces becomes more efficient using optimization algorithms.
Takeaway
When an IC is subjected to loads, it may fail and the mode of failure can vary depending on the load conditions and environment. Therefore, it is important to identify the most significant parameter that contributes to IC failure under different circumstances. FEA simulations can accurately replicate IC failure and analyze the primary causes of wirebond failure under various conditions. It should be noted that wire bonding path plays a critical role in wirebond durability. By performing realistic simulations using Abaqus FEA, one can find the optimal parameter for the best design of IC.

Car Mirror Chattering CAE Analysis
While driving a car at high speed or through the bumpy road surfaces, the rear-view and side-view mirror surface happens to vibrate. Once the vibration frequency hit the resonance frequency of the mirror, it will leads to blurry images reflected from the mirror and affect sight of the drivers to clearly identify the approaching vehicles from the rear.
By performing Modal Analysis using Abaqus, the resonant frequencies and chattering angle of the car mirror due to different vibration directions can be identified. By comparing the results from simulation and testing, simulation settings can be refined to close the gap between the results from simulation and testing. Through observing the vibration pattern of the mirror simulated by using Abaqus, design optimization (if needed) which includes geometry / material changes can be done with the aim to pass the test requirements and reduce the material cost.
Frequently Asked Questions
With reference to the industry organizations such as JEDEC and the IEC standards and guideline, plus the aid of microscopic images and x-ray, one can easily replicate the IC, chips and other components.
The FEA simulations results provide information on the stress distribution, strain, displacement, etc when the IC and other components were under certain loading conditions and environment. The information are used to determine the root cause of the failure of IC other components.
The most frequently spotted failure in IC is the fracture of the wirebond. This could be due to machine setup, excessive wirebond deformation, dirty wire clamps and etc.
Depending on the scope, the charges depend on the man-day and measurement services included. We are very transparent on the charges. Please contact us to find out more.
The industries that work with integrated circuit such as electronics, automotive, aerospace and defenses, telecommunication and etc.
I-Sight is a software tool commonly utilized alongside Abaqus to facilitate automated simulation workflows. It functions as a process integration and design optimization software. Through its user-friendly graphical interface, I-Sight enables users to define simulation workflows, including input parameters, and effectively manages the execution of Abaqus simulations according to the specified workflow.
Growth is Hard, But We’ve Got You
Don’t hesitate and book your call today to change the future.
Related Product
We start with the end in mind, together with qualitative and quantitative data collection and analysis, we create a business strategy that ensure our clients achieve their goals and experience measurable values.
ABAQUS
The Abaqus Unified FEA product suite offers powerful and complete solutions for both routine and sophisticated engineering problems covering a vast spectrum of industrial applications.
Key Takeaways
Lorem ipsum dolor sit amet, consectetur adipiscing elit, sed do eiusmod tempor incididunt ut labore et dolore.
Lorem ipsum dolor sit amet, consectetur adipiscing elit, sed do eiusmod tempor incididunt ut labore et dolore.
Lorem ipsum dolor sit amet, consectetur adipiscing elit, sed do eiusmod tempor incididunt ut labore et dolore.
Lorem ipsum dolor sit amet, consectetur adipiscing elit, sed do eiusmod tempor incididunt ut labore et dolore.
Lorem ipsum dolor sit amet, consectetur adipiscing elit, sed do eiusmod tempor incididunt ut labore et dolore.
Lorem ipsum dolor sit amet, consectetur adipiscing elit, sed do eiusmod tempor incididunt ut labore et dolore.